智能精准公差计算软件一键快速优化工程设计流程
19429202025-03-21绿色软件38 浏览
传统公差设计:效率与精准能否兼得?
在机械制造领域,公差设计是决定产品质量和生产成本的关键环节。传统公差分析依赖工程师手工计算和经验判断,不仅耗时耗力,还可能因人为误差导致设计返工甚至产品失效。据统计,约30%的制造缺陷源于公差分配不合理。面对日益复杂的产品结构和高精度需求,工程师们不禁发问:是否存在一种工具,既能一键优化设计流程,又能确保精准可靠?
1. 效率瓶颈如何突破?
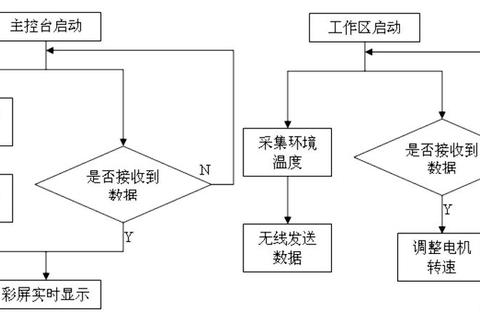
传统公差分析需工程师逐一对尺寸链建模、计算公差累积效应,动辄耗费数周时间。例如,某火箭电控箱设计中,需分析数百个电子元件与水冷板的间隙公差,手动建模需10-15天,而智能精准公差计算软件(如DTAS 3D)通过AI自动建模技术,仅需10分钟即可完成265个特征和65项公差的仿真模型搭建,效率提升80%。这种“一键生成”功能不仅缩短周期,还标准化了建模流程,减少人为疏漏。
案例支撑:某航天企业采用DTAS 3D的AI模块后,电控箱公差分析周期从2周压缩至1天,成功规避了因公差导致的散热失效风险,项目交付时间提前30%。
2. 复杂装配如何确保零缺陷?
精密装配场景中,公差叠加效应可能导致运动干涉或功能失效。以某医疗器械的连杆机构为例,理想状态下V型摇杆旋转角度需严格控制在±0.5°内,但实际制造偏差会导致中分面角度波动。传统人工计算无法动态模拟运动路径的极限状态,而智能软件通过虚拟装配迭代和组合限位算法,精准预测最大偏差,并自动优化公差分配方案。
数据对比:某企业使用CETOL 6σ软件分析某汽车发动机缸体,发现原设计公差导致装配失败率高达12%。通过灵敏度分析调整关键尺寸公差后,失败率降至0.5%,年度返工成本减少500万元。
3. 中小企业如何低成本转型?
高端公差软件动辄百万元授权费,常令中小企业望而却步。国产软件(如DTAS、DCC)以高性价比破局:重庆某非标设备厂商采用DCC尺寸链计算软件,仅投入5万元即实现公差分析自动化,设计错误率降低60%。这类软件提供灵活的模块化服务,企业可按需采购基础功能,后续逐步扩展。
行业趋势:2024年AI技术加速融入国产软件,例如DTAS 3D新增的偏差渲染功能,可直观展示公差对产品外观的影响,帮助设计师快速决策。
行动建议:三步实现设计流程升级
1. 需求评估:根据产品复杂度选择工具。简单零件可尝试Excel插件(如公差查询工具),复杂装配推荐3DCS、CETOL或DTAS 3D等专业软件。
2. 试用验证:多数软件提供免费试用期,优先测试AI建模、动态仿真等核心功能。
3. 人才培养:联合软件供应商开展培训,重点掌握统计公差分析、根源诊断等进阶技能。
智能精准公差计算软件一键快速优化工程设计流程,正从“可选工具”变为“必备基建”。无论是航天重器还是微型医疗器械,只有将公差控制从经验驱动转向数据驱动,才能在质量与成本之间找到最优解。正如某工程师所言:“用好公差软件,相当于给设计装上‘防错保险’。”