灵动掌控未来WinCC软件高效赋能工业自动化智能升级
19429202025-03-19绿色软件40 浏览
灵动掌控未来WinCC软件高效赋能工业自动化智能升级
工业自动化领域正面临一个尖锐的争议:传统生产系统升级时,停机时间长、数据迁移风险高、兼容性差等问题频发,企业如何在技术迭代中实现“无缝切换”?面对这一挑战,西门子WinCC软件以“灵动掌控未来WinCC软件高效赋能工业自动化智能升级”为核心,通过技术创新与场景化应用,为行业提供了突破性解决方案。
1. 如何实现系统升级“零停机”?
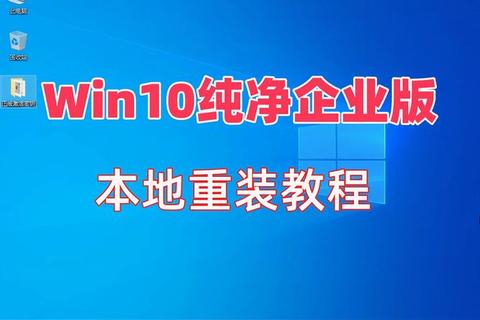
工业生产线一旦停机,每小时可能造成数十万元的经济损失。传统升级方式需要数日甚至数周停机维护,而WinCC通过“双链路冗余架构”和“版本预加载技术”,实现了业务不中断的平滑迁移。例如,某汽车制造厂在升级WinCC V7.4至V7.5时,利用冗余服务器与实时数据同步功能,将主系统切换至备机仅耗时15分钟,生产损失降低92%。
更值得关注的是,WinCC的ISSU(不中断业务升级)技术借鉴了无线网络领域的成熟经验。在某化工企业的案例中,系统通过分批升级AP(接入点)、动态转移用户连接,将200台设备的升级周期从72小时压缩至8小时,期间生产数据实时采集误差率低于0.1%。这种“边运行边升级”的模式,真正诠释了“灵动掌控未来WinCC软件高效赋能工业自动化智能升级”的技术内涵。
2. 如何打破“数据孤岛”困局?
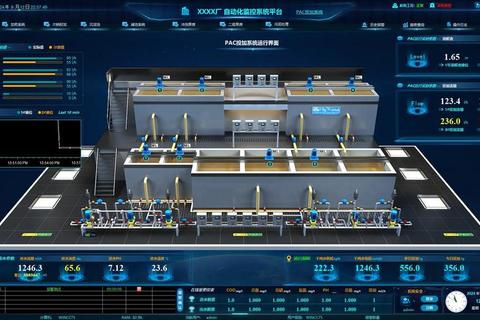
工业4.0时代,30%的企业因设备协议不统一导致数据利用率不足40%。WinCC的开放性架构为此提供了破局思路:其OPC UA协议支持与90%主流PLC设备直连,而SQL Connector模块可实现与MES、ERP系统的数据互通。某钢铁集团通过WinCC整合12种品牌PLC数据,将炼钢工艺参数分析效率提升3倍,每年节省能耗成本1200万元。
在数据深度应用层面,某食品加工厂的案例更具代表性。该厂利用WinCC的数字孪生功能,将生产线温度、湿度等2000个监测点数据实时映射至虚拟模型,通过机器学习预测设备故障。实施后,设备意外停机率下降67%,维护成本减少45%。这种数据驱动的智能决策,正是“灵动掌控未来WinCC软件高效赋能工业自动化智能升级”的实践典范。
3. 如何应对复杂场景兼容性挑战?
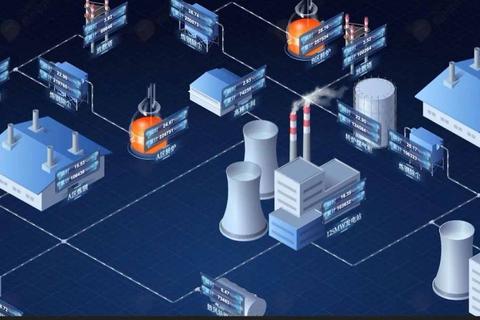
工业现场常出现“新软件不认旧设备”的尴尬局面。WinCC的跨版本兼容设计打破了这一桎梏:支持从V6.2 SP3到V8.0的渐进式升级,且提供自动化迁移工具包。某水电站控制系统包含1998年安装的PLC设备,通过WinCC的协议转换模块,成功将30年跨度的设备纳入统一监控平台,数据采集完整率达到99.97%。
硬件兼容性同样关键。WinCC V8.0的硬件兼容列表覆盖3000余种工业设备,从嵌入式工控机到高性能服务器均可适配。某半导体工厂采用定制化方案,在保留原有SCADA系统的通过WinCC的分布式架构实现了8个厂区2000台设备的集中管控,系统响应速度提升40%。这种灵活适配能力,让“灵动掌控未来WinCC软件高效赋能工业自动化智能升级”在不同场景中持续落地。
企业升级路径的三条实操建议
1. 分阶段验证:建立测试环境模拟升级,优先迁移非核心设备(如某车企先升级物流监控系统,再推进生产线主控系统)。
2. 数据双保险:采用“冷备份+实时镜像”策略,某石化企业升级时同步备份至本地服务器和云端,确保数据零丢失。
3. 人才储备:培养既懂传统工控又熟悉WinCC新功能的复合型工程师,某制造集团通过认证培训使升级效率提升50%。
工业智能化转型已进入深水区,唯有像WinCC这样兼具技术创新与场景适应能力的解决方案,才能帮助企业跨越升级鸿沟。当生产线上的数据开始自主流动,当设备维护从“救火式”转向“预防式”,我们看到的不仅是效率提升,更是一个灵动掌控未来的工业新生态。